Kanban Metrics: How To Measure Kanban Work & Efficiency
Kanban metrics are vital tools for gauging work process effectiveness. They serve as a compass, providing clear directions towards improving productivity by tackling tasks strategically. These four core metrics - Lead Time, Cycle Time, Work-in-Progress (WIP), and Throughput - lay the groundwork for understanding the pulse of any work process. Notably, achieving maximum productivity isn't always about speeding up; sometimes, it may require slowing down, focusing more on one task at a time rather than juggling multiple. Let's start with the basics.
The essential Kanban metrics include lead time, cycle time, work-in-progress, and throughput. Lead time measures the time from task addition to completion, while cycle time measures the duration from task start to finish. Work-in-progress helps manage active tasks, and throughput quantifies completed tasks within a specific timeframe. These metrics are crucial for identifying bottlenecks, improving forecasting, and maximizing efficiency across projects.
To effectively enhance your Kanban workflow, it is crucial to focus on key metrics such as board, results, WIP limit, backlog, velocity, defect rate, and data analysis. Following this critical rule, understanding and actively managing these metrics becomes essential for optimizing business throughput and minimizing wastes within your Kanban team.
Knowing and honing in on the right key Kanban metrics is paramount for the continuous improvement of your Kanban workflow. By incorporating elements such as board, results, WIP limit, backlog, velocity, defect rate, and data analysis, you empower your team to systematically assess performance and drive improvements, ultimately fostering increased efficiency and reduced waste in the Kanban process.
The Four Essential Kanban Metrics
Kanban introduces a set of vital metrics that provide critical insights into project management and workflow performance. These metrics offer clear indicators of productivity and efficiency, shaping the framework for continuous improvement within an organization. Understanding these essential Kanban metrics is key to effectively measuring and optimizing workflow processes. Let's explore each of these detailed Kanban metrics one by one.
Kanban Metric #1. Lead Time
Lead time measures the duration from when a task is added to the system until it's marked as complete. This metric provides a comprehensive understanding of how long it takes for a task to move through the entire workflow—right from the customer request to delivery. It unravels the actual time taken for a request or requirement to be fulfilled, providing valuable insights into process efficiency and customer satisfaction.
Kanban Metric #2. Cycle Time
On the other hand, cycle time tracks the time taken from commencing work on a task to its completion. It portrays the actual time spent actively working on a task, offering a microscopic view of operational efficiency within individual tasks or user stories. By dissecting cycle time data, teams can identify potential bottlenecks within specific stages of their workflow, enabling targeted process improvements.
Kanban Metric #3. Work-in-Progress (WIP)
The concept of work-in-progress (WIP) encapsulates the volume of tasks actively in play at any given moment within the workflow. Monitoring WIP allows teams to visualize the workload across different stages, identify clogging points, and enforce work limits to prevent overburdening team members or impeding task flow. Limiting WIP ensures smoother workflow operations and prevents multitasking from hampering productivity.
Kanban Metric #4. Throughput
Finally, throughput measures the quantity of tasks completed within a specific timeframe, typically evaluated weekly or monthly. Throughput metrics provide a macroscopic lens into overall productivity and goal achievement, serving as an overarching indicator of team performance.
By comprehensively understanding and leveraging these essential Kanban metrics, teams can wield actionable data insights to bolster efficiency, streamline workflows, and enhance project output. Transitioning from understanding Kanban metrics, let's now delve into the necessity of implementing these pivotal measurements in organizational workflows.
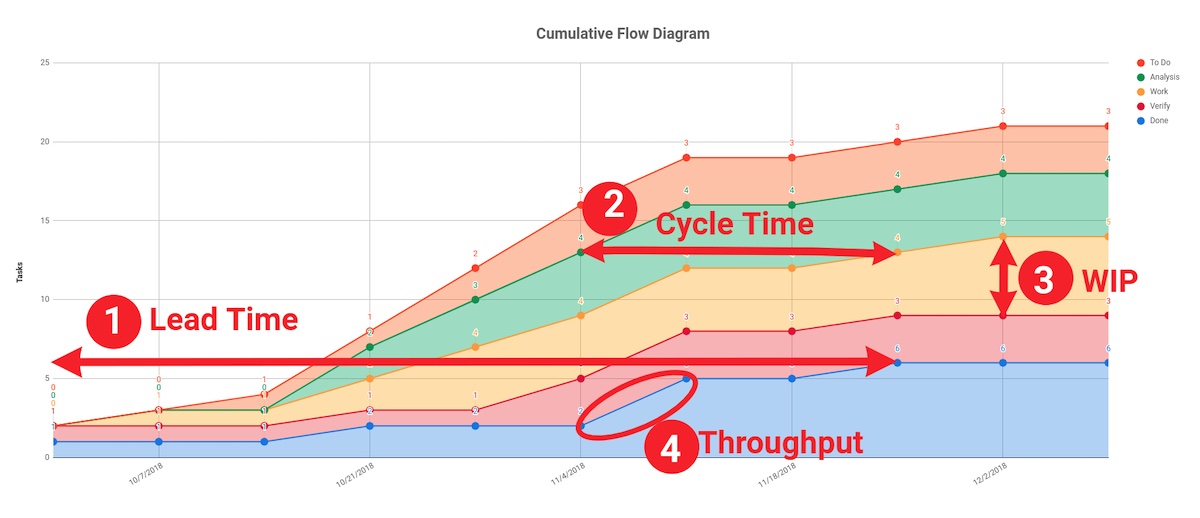
Kanban Metrics
Necessity of Implementing Kanban Metrics
Imagine running a marathon without knowing how far you've come or how far you have left. That's what it's like to run a project without metrics. Implementing Kanban metrics is more than just a good practice; it's a necessity for efficient project management. Let's explore why.
One of the major benefits of implementing Kanban metrics is the ability to identify bottlenecks in workflow. These bottlenecks are like potholes in a road—they slow down progress and cause frustration. By using metrics, teams can pinpoint where these bottlenecks occur. For instance, if lead time or work-in-progress numbers suddenly spike, it could indicate a bottleneck that needs attention.
Another compelling reason for implementing Kanban metrics is the power they hold in forecasting project completion times. Keeping track of lead time, cycle time, and throughput enables teams to create more accurate forecasts for when projects will be completed.
It's not just about identifying problems and forecasting; it's also about increasing overall efficiency. By understanding how long it takes to complete tasks and where they get stuck, teams can implement changes that streamline their work processes.
By embracing Kanban metrics, teams gain valuable insights into their workflow, leading to smarter decisions and improved performance.
The power of Kanban metrics doesn't end with identification and forecasting; let's uncover further advantages in harnessing this vital tool for project management.
Navigating Kanban Metrics for Efficient Workflow Management
Little's Law guides us to properly administer, set client expectations, and continuously improve the Kanban workflow. Little's Law states that:
Cycle Time = Work In Progress (WIP) / Team Throughput
Little's Law shows the correlation between the three key Kanban workflow metrics. Changing one of these metrics will have an impact on the other two metrics.
For instance: To accomplish a reduction in cycle time, Work in Progress (WIP) must decrease, or the Team Throughput must increase.
- Work Item Age: The amount of time a Kanban card in work in progress state spends in the Kanban workfl ow from the moment the Kanban team starts working it until the moment of measurement.
- Problems (Impediments): The number of Kanban cards in the Kanban workflow that cannot be processed or delivered due to blocking dependencies, planning, or all other types of errors.
The excellent point about Kanban metrics is that you can determine the length of your feedback loop, based on how frequently you want to analyze your metrics and make changes in your Kanban workflow.
A long feedback loop indicates that your process improvement will be slow. A short feedback loop suggests that your process may not have sufficient time to stabilize between each change.
The length of the feedback loop in which you observe your metrics is one of the items you can experiment too.
In the domain of Kanban workflow management, understanding key metrics is paramount. Cycle Time, denoted as the duration a work item spends in the Kanban workflow, is intricately tied to the Team Throughput and Work in Progress (WIP). Little's Law serves as a guide for project managers in administering and continuously improving the workflow, emphasizing the importance of setting client expectations. This law highlights the correlation between metrics, stating that changes to one metric will impact the others – for example, reducing cycle time requires a decrease in WIP or an increase in Team Throughput.
Furthermore, examining Work Item Age and addressing Problems (Impediments) in the Kanban workflow are crucial for efficient operations. These metrics are integral to the Kanban board, a visual representation of tasks and their statuses. The burn-up chart, burn-down chart, and throughput histogram provide insightful representations of the project's progress and the team's efficiency. Project managers and team members can utilize these metrics to gauge the length of their feedback loop, influencing the pace of process improvement. A shorter feedback loop encourages more frequent analyses and adjustments, promoting agility and responsiveness within the Kanban methodology. Experimentation with the feedback loop length becomes a valuable tool in optimizing the Kanban workflow for greater productivity.
Effective Tools for Tracking Kanban Metrics
When it comes to tracking Kanban metrics, several effective tools can provide insights into workflow processes and ensure that your team is operating at peak efficiency.
Control Charts
One of the most powerful tools for visualizing variations in process metrics is the control chart. These charts help teams pinpoint areas of process stability and identify abnormalities. They are instrumental in tracking cycle time stability and variability, providing a clear visualization of how processes change over time.
Imagine a control chart like a weather report for your work processes. Just as a weather report provides insight into the variations in temperature and precipitation over time, a control chart tracks variations in your process metrics, such as lead time or cycle time, allowing you to observe patterns and identify any irregularities that may require attention.
Cumulative Flow Diagrams
In addition to control charts, cumulative flow diagrams (CFDs) provide an insightful view of the flow of work items through different stages of the process. These diagrams not only help teams understand the work-in-progress (WIP) but also aid in identifying potential bottlenecks and measuring lead and cycle times.
Let's break this down further. A cumulative flow diagram resembles a dynamic storyboard of your workflow, showing the ebb and flow of tasks as they move through different stages. It provides a layered perspective on not just WIP but also lead and cycle times, helping teams gain valuable insights into their productivity levels and identifying any areas that may be causing delays.
Some might argue that using these tools seems too complex or unnecessary, but when it comes to maximizing efficiency and identifying areas of improvement, having a clear visualization of your process metrics is invaluable.
By leveraging control charts and cumulative flow diagrams, teams can gain valuable insights into their workflow processes, identify areas for improvement, and work towards achieving optimal efficiency in their projects.
Armed with a better understanding of tracking Kanban metrics and the tools at your disposal, let's now explore how to apply these insights to achieve maximum efficiency in project management.
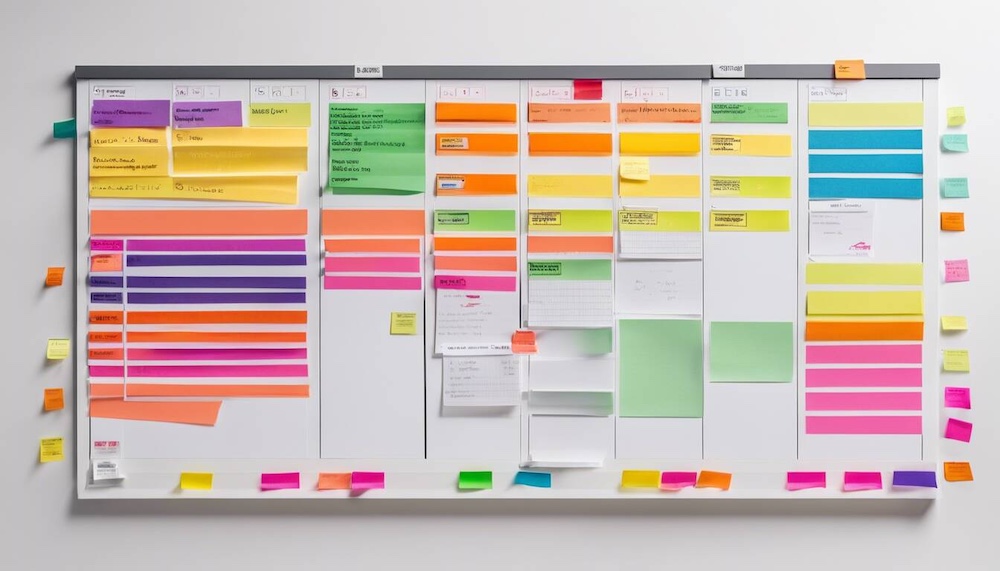
Kanban Metrics Board
Achieving Efficiency with Kanban Metrics
Kanban metrics offer valuable insights that can help streamline your workflow and make informed decisions to improve your team's performance. Let's unpack this further.
Identifying Workflow Inefficiencies
One of the key benefits of using Kanban metrics is the ability to spot where work is getting stuck in your workflow. Lead time and cycle time metrics allow you to see how much time tasks spend in each stage of your process. This visibility enables your team to pinpoint areas where work is slowing down or getting bottlenecked, giving you a clear focus for process improvement efforts.
For instance, if there is a consistent delay in a particular stage of the process, it might indicate a need for additional resources or potential inefficiencies in the current workflow. By using data-driven insights, you can target specific areas for improvement, thereby enhancing the overall efficiency of your team's operations.
Improving Forecast Accuracy
In addition to identifying workflow inefficiencies, Kanban metrics also play a crucial role in improving forecast accuracy. Tracking metrics such as cycle times and throughput enables teams to gain a deeper understanding of their project completion timelines. By analyzing historical performance data, teams can make more accurate forecasts, leading to better planning and more reliable delivery timelines.
For example, if your team consistently completes a certain number of tasks within a specific timeframe, you can use this data to make predictions about future project completions. This allows for better resource allocation and realistic expectations for project delivery, ultimately enhancing the overall efficiency of your project management processes.
By harnessing the power of Kanban metrics to identify workflow inefficiencies and improve forecast accuracy, teams can proactively address operational challenges and cultivate a culture of continuous improvement.
Transitioning from measuring productivity and efficiency with Kanban metrics, let's now explore how these metrics drive quality improvement in project management.
Quality Improvement through Kanban Metrics
When discussing quality improvement through Kanban metrics, we're delving deep into the essence of delivering exceptional work and surpassing customer expectations. Kanban metrics transcend mere numbers; they inform better decision-making that directly impacts the quality and efficacy of the work being produced.
One crucial aspect is identifying defect trends. By tracking metrics like lead time and cycle time, teams can uncover patterns revealing where defects or rework are most likely to occur. This insight is vital as it allows teams to address issues early on, preventing them from snowballing into larger setbacks later.
Using visual management tools such as control charts, teams can visually identify these trends, enabling proactive measures to maintain high quality throughout the project lifecycle. This leads to a more efficient approach to handling defects and ensures that quality issues are nipped in the bud before they escalate.
Additionally, by focusing on cycle times and quality metrics, teams can significantly enhance the overall quality of their deliverables. When cycle time decreases or stabilizes within an acceptable range, it indicates that work items are being completed efficiently without compromising quality. This not only leads to higher-quality output but also enhances customer satisfaction due to timely and reliable delivery.
Enhancing Customer Satisfaction
Kanban metrics play a significant role in boosting customer satisfaction. By continuously monitoring cycle times and quality metrics, teams can ensure that deliverables meet or exceed customer expectations. When customers receive high-quality products or services within expected timelines, it naturally leads to greater satisfaction and fosters long-term relationships.
This goes beyond just delivering something on time; it's about delivering something that customers love—something that works flawlessly and delights them. By utilizing Kanban metrics to ensure consistent quality across deliverables, teams solidify their position as trusted partners in their customers' success.
To sum up, leveraging Kanban metrics for quality improvement is not solely about meeting standards; it's about surpassing them. It's about setting new benchmarks for excellence and consistency in your work—all of which directly contribute to satisfied, loyal customers who recognize your commitment to delivering exceptional value.
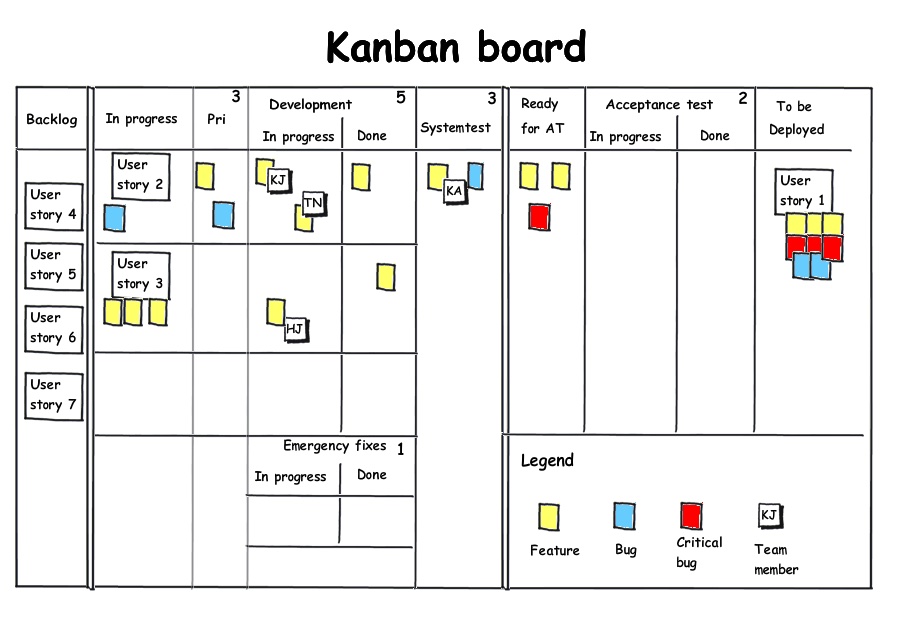
Kanban Metrics Continuous Improvement
Strategizing from Kanban Metrics Outcomes
After diligently measuring and analyzing your team's performance through the lens of Kanban metrics, it's time to put the insight gained into practical use. The purpose is not just identifying where you are, but also shaping where you're headed. Let's explore how you can leverage this knowledge to drive continuous improvement and optimize resource allocation within your team.
Continuous Improvement Through Insightful Analysis
The value of measuring Kanban metrics lies in the ability to uncover opportunities for improvement. By diving deep into cycle time, lead time, work-in-progress, and throughput metrics, you gain visibility into process bottlenecks, inefficiencies, and areas where workflow can be smoothed out. This breadth of insight allows teams to make targeted adjustments and implement changes that directly address the specific pain points revealed by the data.
Such insights facilitate a mindset shift within your team—a collective commitment to continual growth and refinement. It's not about being satisfied with meeting current productivity targets; it's about exploring ways to surpass them by evolving processes over time. For instance, if a key metric highlights a prolonged lead time for certain tasks, it signals an opportunity to rework workflows for quicker task completion, ultimately contributing to enhanced overall efficiency.
Resource Allocation for Optimal Productivity
Another key aspect of incorporating Kanban metrics outcomes into your strategy lies in resource allocation. When armed with precise data regarding throughput, work-in-progress, and cycle time, teams are better equipped to make informed decisions on resource distribution and process adjustments.
Utilizing these insights enables teams to allocate resources efficiently by identifying areas with excessive or limited capacity where adjustments can foster a more balanced distribution. For example, if the analysis identifies a consistent surplus of capacity in one stage of the workflow, it indicates an opportunity to reallocate resources to other stages requiring additional support—a move that might significantly improve overall productivity without increasing resources.
Some may argue that overly detailed scrutiny of the data can lead to paralysis by analysis. However, it's important to remember that the goal is not perfection but optimization. Continuous evaluation and course correction based on comprehensive metrics is crucial in an environment where adaptability and refinement are valued over rigid adherence to dated processes.
Harnessing the power of insightful data provided by Kanban metrics sets the stage for significant improvements in both process efficiency and resource allocation within your team. This marks a pivotal shift from merely gauging performance to actively using that information as a springboard for growth and achievement.
What tools or software can be used to measure and analyze kanban metrics?
Answer: There are several tools and software available to measure and analyze kanban metrics effectively. Some popular options include Kanbanize, LeanKit, and Trello. These tools provide features such as real-time data updates, visual analytics, and customizable dashboards that enable teams to track key metrics like cycle time, lead time, and throughput. According to a study by AgileCraft, organizations that implemented kanban tools experienced a 45% increase in productivity and a 30% decrease in delivery time.
How do kanban metrics help improve workflow efficiency?
Answer: Kanban metrics play a crucial role in improving workflow efficiency by providing valuable insights into the bottlenecks and inefficiencies of the process. By measuring cycle time, lead time, and throughput, teams can identify areas for improvement and implement strategies to reduce wait times and increase productivity. For example, analyzing the average lead time for completing tasks can help in setting realistic expectations with stakeholders and improve resource allocation. Statistics show that organizations that actively measure kanban metrics achieve higher levels of workflow efficiency, with an average reduction of 20% in lead time and a 15% increase in throughput.
How do different teams or organizations approach measuring and interpreting kanban metrics?
Answer: Different teams and organizations approach measuring and interpreting Kanban metrics in various ways. Some focus on cycle time, throughput, and lead time to evaluate productivity and efficiency. Others may prioritize metrics like work in progress (WIP) limits adherence or the number of blocked items to improve workflow management. A study conducted by LeanKit found that teams that consistently measured and analyzed Kanban metrics experienced a 50% increase in productivity within six months. However, it is important for each team or organization to define their own set of metrics based on their specific goals and context, as what works for one may not work for another.
Are there industry-standard benchmarks for kanban metrics?
Answer: Yes, there are industry-standard benchmarks for kanban metrics. The Kanban Method has been widely adopted by industries across the globe, leading to the establishment of metrics that provide a standardized way to measure productivity and efficiency in kanban systems. For instance, Cycle Time is a commonly used metric that measures the time it takes for a task to move from start to finish, providing insights into team performance and process improvements. Additionally, Lead Time and Throughput are widely recognized metrics that help gauge the speed and capacity of delivering work items. These standardized benchmarks provide organizations with a framework for evaluating their performance against industry norms and identifying areas for improvement.
What are the most important metrics to track in a kanban system?
Answer: The most important metrics to track in a kanban system are cycle time, lead time, and throughput. Cycle time measures the amount of time it takes for a card to move from start to finish, providing insights into the team's efficiency. Lead time is the total time taken from a card entering the system until it is completed, giving an overall view of the system's responsiveness. Throughput tracks the number of cards completed in a given timeframe, indicating the team's productivity. These metrics allow teams to identify bottlenecks, optimize workflow, and improve overall performance. According to a study by LeanKit, teams that actively tracked these metrics experienced a 55% increase in productivity and a 45% reduction in lead time.
Kanban Metrics Recap
These four core Kanban metrics are:
- Lead Time
- Cycle Time
- Work-in-Progress (WIP)
- Throughput
In the dynamic landscape of project management, a comprehensive understanding of Kanban metrics is indispensable. These metrics serve as the compass for project managers and teams, guiding them toward efficient workflow management and continuous improvement. Let's delve into a recap of key Kanban metrics that illuminate the path to success.
- Cycle Time and Little's Law: At the core of Kanban metrics lies Cycle Time, a metric intertwined with Work in Progress (WIP) and Team Throughput. Little's Law, a guiding principle, emphasizes the importance of administering the Kanban workflow effectively. Project managers rely on this law to set client expectations and drive continuous improvement. Understanding the correlation between these metrics enables teams to make informed decisions to enhance their workflow.
- Work Item Age and Impediments: Work Item Age and Impediments provide vital insights into the efficiency of the Kanban workflow. The Kanban board, a visual representation of tasks and their statuses, incorporates these metrics. Identifying and addressing impediments ensure a smoother flow of work. The burn-up chart, burn-down chart, and throughput histogram serve as visual aids, offering a clear representation of the project's progress and the team's performance.
- Feedback Loop Optimization: The length of the feedback loop plays a pivotal role in the adaptability and responsiveness of a team. Kanban metrics provide project managers and team members with the tools to gauge and experiment with the feedback loop length. A shorter feedback loop encourages more frequent analyses and adjustments, fostering agility and rapid process improvement. Experimentation becomes a key element in optimizing the Kanban workflow for increased productivity and effectiveness.
In conclusion, the recap of Kanban metrics underscores their role as essential navigational tools in the project management journey. By leveraging these metrics, teams can gain valuable insights, make informed decisions, and continuously refine their processes for optimal performance and success.
Share It With Your Colleagues and Friends to Help Them Learn: Kanban Metrics: How To Measure Kanban Work & Efficiency
|
|
|
|
|
|
|